Art
The art of finishing – Canadian Metalworking
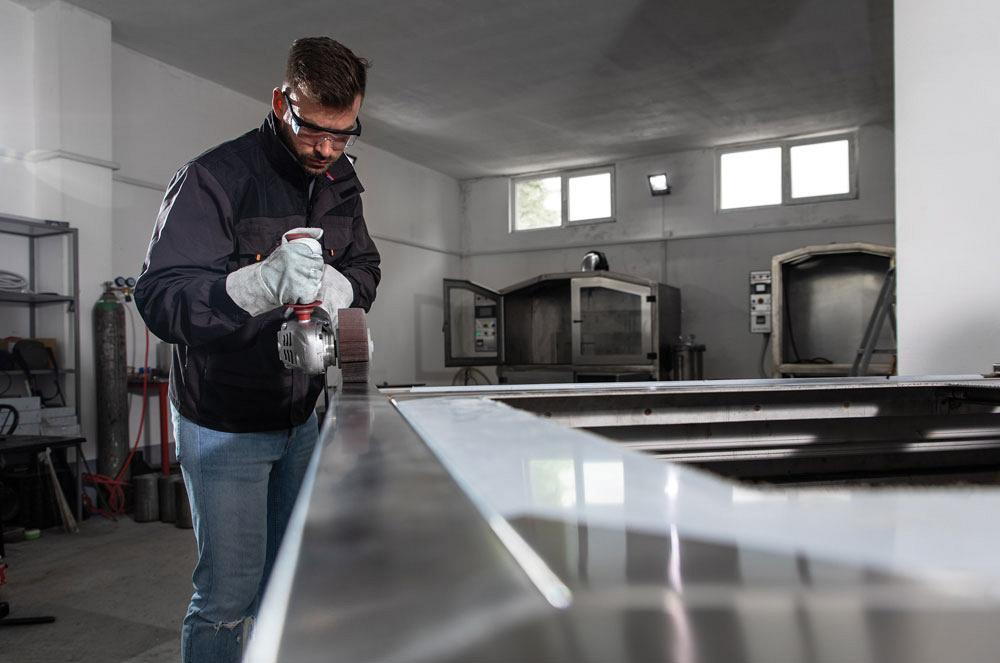
It is so important to use the proper tools when finishing stainless steel, especially because it is so expensive to work with.
It’s almost impossible to go anyplace where stainless steel is not visible. From the banks, airports, motels, restaurants and breweries, and elevators to common handrails, stainless steel is everywhere. Each stainless steel component was carefully crafted with both utilitarian and aesthetics functions in mind. Beyond fabricating and welding a product, metal finishers spend a great deal of time getting the sheets and finished products to look exactly the way a customer wants them.
With the multitude of finishes that can be produced, the experts agree that it is the No. 4 finish that is the most popular on the market today. It is truly the workhorse finish of finishes.
“The No. 4 finish is by far the most popular finish that shops produce and customers are asking for,” said Steve Bell, Quebec territory manager, PFERD Canada Inc., Mississauga, Ont. “It was originally designed for the food industry as it does not leave pit marks where bacteria can collect. Instead it is an easy-to-clean surface. However, it also offers a very aesthetically pleasing grain finish, making it more common for other industries and projects.”
And although the No. 4 finish is by far the most common, there are dozens of other finishes that customers may request for their products.
“Many other finishes have come out over the years,” said Randy McDonald, applications specialist, Fein Canada, Mississauga, Ont. “The No. 4 finish has also been adapted to create a No. 4 family of finishes, which offer slight variations. Other commonly requested finishes include No. 6 and No. 7.”
Providing the right finish to customers can be a challenge, though. One man’s No. 4 finish is not always another’s. Finishes are extremely subjective, and many shops may require extra fine-tuning to get the stainless steel to the exact requirements of the customer.
“I always tell people, the proper finish is a subjective opinion,” said McDonald. “And by that I mean, I can go into a stainless steel shop that is producing No. 4-finish range hoods for restaurant equipment. I can show the shop a couple of wheels and the operator could look at the finish it produces and agree it’s perfect. However, I can go to the shop’s biggest competitor that is making the exact same product, using the same tool, the same wheels, and the operator could look at it and not think it is correct. That’s why it’s important to have a range of abrasives to account for the opinion factor, where shops can make the finish a little grainier or more satiny depending on customer needs.”
Finishing can be time-consuming, and shops might have to take many different steps to get it right. It’s not an exact science, especially because of the human factor, both from the operator’s ability and the end user’s acceptance of the finish.
“It’s really important for each shop to ask questions to its customer about exactly what they are looking for in a finish,” said Bell. “We often see shops spend extra time overfinishing a product, which can be unnecessary.”
Common stainless steel finishes
No. 2B—Standard mill finish, smooth grey reflective sheen from the factory. It is cold-rolled, heat-treated, and pickled with a skin pass. This is most widely used as a base material for most polished or brushed finish applications.
Because of all the different finishes and the incredibly wide range of abrasives available, a shop must have variable-speed tools and tools that provide the right speed range for the abrasives being used. Photo courtesy of Fein.
No. 4—Inline brushed finish, sometimes referred to as a food-grade finish. It is not reflective and can be in the 120- to 180-grit range, depending on the manufacturer. It is used extensively in food, dairy, pharmaceutical, and process equipment where a smooth sanitary finish is required.
No. 6—Inline satin brush finish, finer and softer than the No. 4 finish. This can be a subjective finish ranging from 320 to 600 grit, depending on the customer’s expectations.
No. 7 or 8—Mirror finish, absolutely no lines and very reflective with a high degree of clarity. It is obtained by using finer-grit abrasives in various steps and then with buffs and compounds. Typically used for architectural, ornamental, and mirror applications.
New to Finishing Stainless
Working with stainless steel requires precision and skill. Some shops think they can just jump into fabricating stainless steel on a whim, whether that’s because they want to expand the business or because they’ve been asked to. Whatever the reason, shops need to seriously consider all the factors that go into working with stainless.
“You really have to be skilled,” said McDonald. “It’s not like you can just take somebody in off the street, hand them a polishing tool, and expect good results. A welder or worker that is working with mild steel cannot be expected to be familiar with the intricacies of stainless. It’s different. It takes different machines and different equipment.”
The experts agree that the first place to start is reaching out to well-known abrasives and finishing tool manufacturers. A representative can come into the shop to see what exactly the requirements are and help choose the right tools and process to get the job done right. They can also help train workers on the best system for finishing and abrasives. This can save an incredible amount of time and frustration.
When first starting out in stainless, it’s important to note that not all mills create finishes the same way. There is no one-size-fits-all mill-finished stainless steel.
“Each mill has its own particular process of obtaining their particular finish,” said Bell. “When we talk of a No. 4 finish, the grit range can be anywhere from 120 to 320, depending on the project requirements. The higher the grit, the finer the lines and the more reflective the surface will be. If stock runs out or a shop is using material from two different mills, it may be required to refinish the surfaces to match. In order to do this, we recommend having multiple different tools and abrasives on hand to help get that nice matched result.”
All About the Tools
There are basically two types of finishes: rotational (created by an angle grinder pointed downward) and linear (created by peripheral grinding, producing a linear scratch pattern). Shops should start with a rotational finish to break down the weld and then move to a linear finish to get the finish just right.
“However, it’s really all about experimentation,” said Bell. “It’s hard to give recommendations without seeing the workpiece. But the key to remember when finishing stainless is making the right choice on grits; too rough a grit creates deeper microgrooves in the surface, which will take more steps to remove. Another consideration is the type of abrasive grain. Each type of grain has its own characteristics with certain finishing advantages and disadvantages. Experimentation is a great opportunity to discover the look and finish that you can offer your customers. Testing different grits, in both coated and nonwoven products, will change the look and provide more options.”
There is no one-size-fits-all finishing tool that a shop can use to magically achieve the required finish. With many different tools and steps needed, shops can become overwhelmed with choosing the right options. However, there are some recommendations that can help shops effectively finish.
“An absolute must for any shop is dedicated polishing/finishing tools with variable speed for stainless steel,” said McDonald. “Because of all the different finishes and the incredibly wide range of abrasives available, a shop must have variable-speed tools and tools that provide the right speed range for the abrasives being used. This is the most critical choice when you are finishing, particularly from a safety standpoint. Tools with constant speed and constant torque work the best and provide the best finishes.”
All finishing abrasives run at a much lower RPM than a grinding wheel, sanding disc, or flat disc. Standard grinders can run up to 10,000 RPM, whereas most finishing products need to be run around the 3,000-RPM range or lower. If a shop tries to use a fleece-type wheel on a grinder that’s running 10,000 RPM, it could blow up and seriously hurt somebody. It could also burn and discolour the material, causing warpage. Once this occurs, it is very hard to fix and most often the part will be scrapped.
“Finding the right tools, abrasives, conditioning discs, and finishing belts and drums depends on what the customer is looking for,” said Bell. “Having a range of different grits and hand tools readily available can help a shop avoid any finishing issues. Even hand pads can be used at the final stage to help camouflage any finishing inconsistencies.”
It is so important to use the proper tools when finishing stainless steel, especially because it is so expensive to work with.
“I do get into debates with people about the difference between electric tools and air tools,” said McDonald. “The problem with air is that the speed of the tool is dependent on the air pressure supplied, which can be inconsistent. You don’t get the constant speed or constant torque needed. Whereas with electric tools, there are specific tools out there that have absolute constant speed and constant torque because they have a double-gear-reduction system. This is a must for proper finishing. It makes a huge difference. The right tool and right abrasives can all have an effect on the finish that you’re trying to produce or replicate.”
Troubleshoot Challenges
Practice makes perfect. It may be difficult to practice in a demanding work environment, but it can also bring the best results and save the company a lot of time and money in the long term. Getting the proper training for employees can help minimize problems down the road. But sometimes challenges are unavoidable.
Keeping the stainless area or shop separate from other materials is essential. Shops don’t want to mix stainless with carbon steel and certainly don’t want the tools being used on both. Cross-contamination can cause rust on stainless. Having a dedicated area for finishing stainless that is contaminant-free and having dedicated tools can help start the process off right.
When working with stainless, shops can either purchase the stainless with the intended finish or they can purchase a less expensive finish and then finish it in shop. For example, it’s much less expensive to buy a No. 2B finish, cut and bend the material into the product, and then finish in shop. However, not all shops have the skill or experience to do this effectively, so they will purchase the stock in the appropriate finish.
“For example, you can purchase a No. 4 finish from the mill,” said McDonald. “It will be more expensive, but it is a perfect No. 4 finish. There are a few things that shops are required to do in order to maintain the finish throughout the fabrication process. Mishandling of stainless steel, whether it is mill-finished or in-house-finished, is one of the biggest problems. If the material is not clamped properly, it can move and cause an inconsistent finish; if tools are left on the material, it could scratch the material. Keeping the work area clean and properly handling the workpiece are musts for properly finishing stainless.”
It’s also important to note that many No. 4 mill-finish stainless steel sheets come with tape on them for protection. Some shops take this tape off when they go to work with the sheet. McDonald recommends keeping it on and removing only a small section at a time where finishing is required. Even when clamping, just a small area of tape needs to be removed; that way the operator only needs to clean up and finish that small area.
“Metal finishing is an art, and each metal finisher is an artist, so that’s why it’s so important to experiment,” said Bell. “Just like a painter has his own palette of colours and tools that he uses, the same is true for each metal finisher. Getting the right finish can be challenging, and there are many things to consider. But practicing and following expert advice can help shops achieve proper finishing results.”
Associate Editor Lindsay Luminoso can be reached at lluminoso@canadianfabweld.com.
Fein, fein.com
PFERD Canada, www.pferdcanada.ca
Art
Calvin Lucyshyn: Vancouver Island Art Dealer Faces Fraud Charges After Police Seize Millions in Artwork
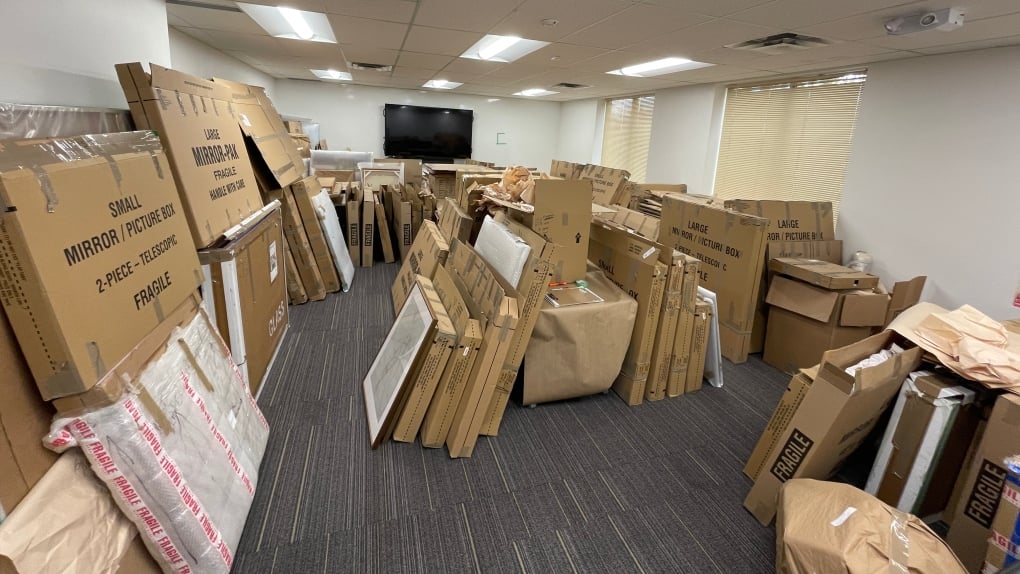
In a case that has sent shockwaves through the Vancouver Island art community, a local art dealer has been charged with one count of fraud over $5,000. Calvin Lucyshyn, the former operator of the now-closed Winchester Galleries in Oak Bay, faces the charge after police seized hundreds of artworks, valued in the tens of millions of dollars, from various storage sites in the Greater Victoria area.
Alleged Fraud Scheme
Police allege that Lucyshyn had been taking valuable art from members of the public under the guise of appraising or consigning the pieces for sale, only to cut off all communication with the owners. This investigation began in April 2022, when police received a complaint from an individual who had provided four paintings to Lucyshyn, including three works by renowned British Columbia artist Emily Carr, and had not received any updates on their sale.
Further investigation by the Saanich Police Department revealed that this was not an isolated incident. Detectives found other alleged victims who had similar experiences with Winchester Galleries, leading police to execute search warrants at three separate storage locations across Greater Victoria.
Massive Seizure of Artworks
In what has become one of the largest art fraud investigations in recent Canadian history, authorities seized approximately 1,100 pieces of art, including more than 600 pieces from a storage site in Saanich, over 300 in Langford, and more than 100 in Oak Bay. Some of the more valuable pieces, according to police, were estimated to be worth $85,000 each.
Lucyshyn was arrested on April 21, 2022, but was later released from custody. In May 2024, a fraud charge was formally laid against him.
Artwork Returned, but Some Remain Unclaimed
In a statement released on Monday, the Saanich Police Department confirmed that 1,050 of the seized artworks have been returned to their rightful owners. However, several pieces remain unclaimed, and police continue their efforts to track down the owners of these works.
Court Proceedings Ongoing
The criminal charge against Lucyshyn has not yet been tested in court, and he has publicly stated his intention to defend himself against any pending allegations. His next court appearance is scheduled for September 10, 2024.
Impact on the Local Art Community
The news of Lucyshyn’s alleged fraud has deeply affected Vancouver Island’s art community, particularly collectors, galleries, and artists who may have been impacted by the gallery’s operations. With high-value pieces from artists like Emily Carr involved, the case underscores the vulnerabilities that can exist in art transactions.
For many art collectors, the investigation has raised concerns about the potential for fraud in the art world, particularly when it comes to dealing with private galleries and dealers. The seizure of such a vast collection of artworks has also led to questions about the management and oversight of valuable art pieces, as well as the importance of transparency and trust in the industry.
As the case continues to unfold in court, it will likely serve as a cautionary tale for collectors and galleries alike, highlighting the need for due diligence in the sale and appraisal of high-value artworks.
While much of the seized artwork has been returned, the full scale of the alleged fraud is still being unraveled. Lucyshyn’s upcoming court appearances will be closely watched, not only by the legal community but also by the wider art world, as it navigates the fallout from one of Canada’s most significant art fraud cases in recent memory.
Art collectors and individuals who believe they may have been affected by this case are encouraged to contact the Saanich Police Department to inquire about any unclaimed pieces. Additionally, the case serves as a reminder for anyone involved in high-value art transactions to work with reputable dealers and to keep thorough documentation of all transactions.
As with any investment, whether in art or other ventures, it is crucial to be cautious and informed. Art fraud can devastate personal collections and finances, but by taking steps to verify authenticity, provenance, and the reputation of dealers, collectors can help safeguard their valuable pieces.
Art
Ukrainian sells art in Essex while stuck in a warzone – BBC.com
[unable to retrieve full-text content]
Ukrainian sells art in Essex while stuck in a warzone BBC.com
Source link
Art
Somerset House Fire: Courtauld Gallery Reopens, Rest of Landmark Closed
The Courtauld Gallery at Somerset House has reopened its doors to the public after a fire swept through the historic building in central London. While the gallery has resumed operations, the rest of the iconic site remains closed “until further notice.”
On Saturday, approximately 125 firefighters were called to the scene to battle the blaze, which sent smoke billowing across the city. Fortunately, the fire occurred in a part of the building not housing valuable artworks, and no injuries were reported. Authorities are still investigating the cause of the fire.
Despite the disruption, art lovers queued outside the gallery before it reopened at 10:00 BST on Sunday. One visitor expressed his relief, saying, “I was sad to see the fire, but I’m relieved the art is safe.”
The Clark family, visiting London from Washington state, USA, had a unique perspective on the incident. While sightseeing on the London Eye, they watched as firefighters tackled the flames. Paul Clark, accompanied by his wife Jiorgia and their four children, shared their concern for the safety of the artwork inside Somerset House. “It was sad to see,” Mr. Clark told the BBC. As a fan of Vincent Van Gogh, he was particularly relieved to learn that the painter’s famous Self-Portrait with Bandaged Ear had not been affected by the fire.
Blaze in the West Wing
The fire broke out around midday on Saturday in the west wing of Somerset House, a section of the building primarily used for offices and storage. Jonathan Reekie, director of Somerset House Trust, assured the public that “no valuable artefacts or artworks” were located in that part of the building. By Sunday, fire engines were still stationed outside as investigations into the fire’s origin continued.
About Somerset House
Located on the Strand in central London, Somerset House is a prominent arts venue with a rich history dating back to the Georgian era. Built on the site of a former Tudor palace, the complex is known for its iconic courtyard and is home to the Courtauld Gallery. The gallery houses a prestigious collection from the Samuel Courtauld Trust, showcasing masterpieces from the Middle Ages to the 20th century. Among the notable works are pieces by impressionist legends such as Edouard Manet, Claude Monet, Paul Cézanne, and Vincent Van Gogh.
Somerset House regularly hosts cultural exhibitions and public events, including its popular winter ice skating sessions in the courtyard. However, for now, the venue remains partially closed as authorities ensure the safety of the site following the fire.
Art lovers and the Somerset House community can take solace in knowing that the invaluable collection remains unharmed, and the Courtauld Gallery continues to welcome visitors, offering a reprieve amid the disruption.
-
Sports19 hours ago
Cavaliers and free agent forward Isaac Okoro agree to 3-year, $38 million deal, AP source says
-
Sports19 hours ago
Liverpool ‘not good enough’ says Arne Slot after shock loss against Nottingham Forest
-
News19 hours ago
k.d. lang gets the band back together for Canadian country music awards show
-
Sports4 hours ago
Armstrong scores, surging Vancouver Whitecaps beat slumping San Jose Earthquakes 2-0
-
News19 hours ago
NATO military committee chair, others back Ukraine’s use of long range weapons to hit Russia
-
News19 hours ago
With a parade of athletes on Champs Elysées, France throws one last party for the Paris Olympics
-
News19 hours ago
‘Challenges every single muscle’: Champion tree climber turns work into passion
-
News4 hours ago
As plant-based milk becomes more popular, brands look for new ways to compete